Comment verdir les métaux ?
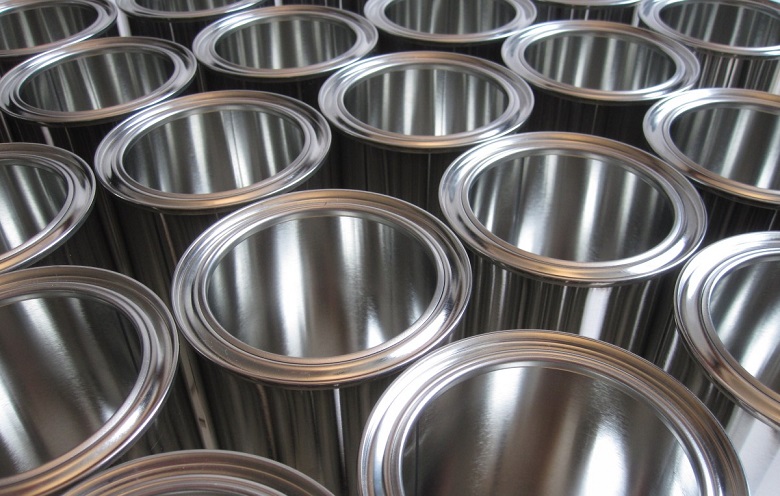
Nous consommons sans vraiment nous en apercevoir des kilogrammes de métaux. Nos automobiles sont lourdes d’acier et d’aluminium, la structure de nos ponts est riche en acier, nos canettes de coca ou de bière sont des enveloppes fines d’aluminium ou d’acier.
Avec le rebond de l’activité industrielle après la pandémie, les productions des deux principaux métaux sont reparties à la hausse en 2021. 1,95 milliard de tonnes pour l’acier (dont 1 milliard pour la Chine) et 64 millions de tonnes pour l’aluminium (dont 26 pour la Chine). Ces productions s’accompagnent d’émissions de gigatonnes de gaz carbonique (1). Les experts calculent que ces deux industries métallurgiques représentent entre 7 et 9 % des émissions planétaires.
Un peu de chimie
On peut comprendre facilement que la réduction des oxydes, que sont les minerais, par le carbone produit du CO2.
Pour l’acier (2a et 2b) et donc le fer, la réduction se fait dans des hauts fourneaux. Le minerai mélangé au coke dans le haut du fourneau, rencontre en descendant le gaz réducteur CO qui résulte de la réaction entre l’air chaud insufflé par le bas de la cuve à haute température suivant la réaction
2C + O2 → 2CO. Les réductions observées sont :
En dessous de 620°C : 3 Fe2O3 + CO → 2 Fe3O4 + CO2
Entre 620° et 950°C, on observe Fe3O4 + CO → 3 FeO + CO2
Puis au-dessus de 950°C : FeO + CO → Fe + CO2
Au sein du haut fourneau, à haute température, le monoxyde de carbone est régénéré à chaque fois que CO2, produit par les réactions précédentes, rencontre une couche de coke selon l’équilibre, dit de Boudouard, C + CO2 →2 CO.
La fonte, fer liquide ayant dissout un peu de carbone, coule dans le bas de la cuve vers 1800 °C. Les gaz ressortent en haut du haut fourneau et contiennent entre autres du dioxyde de carbone. Finalement, pour une tonne d’acier se dégagent 2,2 tonnes de CO2.
Pour l’aluminium, après traitement préalable du minerai (la bauxite) afin obtenir l’oxyde Al2O3, la réduction finale se passe en milieu fondu. Al2O3 est dissout dans un bain fluoré contenant la cryolithe AlNa3F6 et du fluorure de calcium CaF2. L’électrolyse à 960°C conduit au dépôt d’aluminium sur l’électrode de graphite et la réaction s’écrit 2 Al2O3 + 3 C → 4 Al + 3 CO2.
Le procédé conduit à l’émission d’environ 4 tonnes de CO2 par tonne d’aluminium auxquelles il faut ajouter l’empreinte carbone des 12 à 14 MWh nécessaires à l’électrolyse. On comprend donc dans la perspective de la neutralité carbone en 2050 que la recherche et le développement de procédés émettant moins de CO2 soient d’actualité.
L’acier vert
Plusieurs voies sont ouvertes pour diminuer les rejets de CO2 :
- La réduction directe du minerai (DRI ou Direct Reduction Iron) par des gaz chauds à 900°C, gaz naturel (méthane, CH4) ou hydrogène H2 (3) selon :
Fe2O3 + 3 H2 → 2 Fe + 3 H2O ou Fe2O3 + CH4 → 4 Fe + 2 H2O + CO - Si l’hydrogène est vert (4) ou peu carboné (5) la réduction d’émission est supérieure à 80% et pour le gaz naturel à plus de 50%. Les éponges de DRI sont ensuite fondues et purifiées au four à arc électrique.
- L’injection de gaz ou d’hydrogène dans le haut fourneau ou la réinjection d’un mélange CO + H2 permet de réduire de 20 à 30% les émissions.
- La capture et le stockage du CO2 à la sortie du haut fourneau (CCUS ou Carbon Capture Utilization and Storage) permet un gain de 63% sur les émissions.
- Ou mieux encore convertir les gaz sidérurgiques CO et CO2 en éthanol par bio transformation.
De nombreux projets voient le jour en Europe, ArcelorMittal compte investir 10 Mrds € d’ici 2035 pour réduire d’au moins 30% son empreinte carbone. Déjà le consortium Hybrit a fourni au constructeur Volvo en Suède 25 tonnes d’acier vert par réduction directe (DRI) de minerai fourni par le minier LKAB et de l’hydrogène fourni par hydroélectricité de Vattenfall. La France n’est pas mal placée avec l’association Arcelor-Air liquide et le nucléaire pour produire l’hydrogène bas carbone. Il n’en reste pas moins que les volets énergétique et financier sont de vrais casse-têtes. On estime que la décarbonatation du secteur exigera plus de 50 Mrds€ d’investissement et près de 400 TWh d’électricité renouvelable dont 250 pour produire 6,5 millions de tonnes d’hydrogène. Devant cette énorme défi les sidérurgistes rappellent qu’ils sont déjà les champions de l’acier vert puisque plus de 45 % des ferrailles sont recyclées dans les fours à arc électrique, qui certes consomment du carbone, mais n’émettent que 0,3 à 0,6 tonne de CO2 au lieu de 2,2 tonnes pour l’acier brut.
L’aluminium vert
Pour la France Péchiney a été historiquement le berceau de la production (6a et 6b) et (7) avec des cuves d’électrolyse dont il a été le leader pendant longtemps et une production d’aluminium dans les vallées alpines et pyrénéennes profitant de l’électricité issue des barrages hydrauliques de montagne ce qui « verdissait » sa production avant l’heure. Le procédé Hall-Héroult, malgré les progrès sur le rendement électrique atteignant près de 95% sur les dernières cuves C 60, arrive dans ses ultimes années car même avec un mix électrique français favorable on émet 3,5 t de CO2, par tonne d’aluminium, auquel il faut ajouter l’énergie du procédé Bayer pour obtenir l’alumine à partir de la bauxite (7). Dès la fin des années 90, le centre de recherches de Voreppe près de Grenoble se lançait dans l’étude d’électrodes inertes pour remplacer celles en carbone, d’abord métalliques puis céramiques non attaquables dans les bains fluorés (8). Après le rachat de Pechiney par Alcan puis Rio Tinto ces études se sont poursuivies et viennent d’aboutir avec une coentreprise ELYSIS entre Alcoa et Rio Tinto à la construction de cuves prototypes avec des cathodes en cermet comportant une ferrite de nickel substituée capable sous une tension de quelques volts et une intensité de 450 kA, de fournir un aluminium sans carbone. En effet, en l’absence d’électrode en graphite, au sein de l’électrolyseur et en milieu cryolithique fluoré, la réaction est alors Al2O3 → 2 Al + 3/2 O2. De plus, le courant électrique provient des centrales hydrauliques canadiennes, ce qui est une véritable révolution technologique.
Ici encore n’oublions pas que le recyclage de l’aluminium (9) est très important puisque l’aluminium de deuxième fusion représente près de 60% de la production en France en émettant 3 à 10 fois moins de CO2 que l’aluminium primaire et mérite le label « vert ».
Ce recyclage est d’autant plus nécessaire que le coup d’État en Guinée (2e producteur mondial de bauxite après l’Australie) menace l’approvisionnement en bauxite et que la Chine a également nettement diminué sa production en arrêtant un certain nombre de centrales électriques au charbon et en confinant, cause pandémie, une partie de la province chinoise produisant 20 % du métal. Le cours de l’aluminium a ainsi dépassé les 3000 $ /t, son record.
Vite à vos poubelles de couleur pour le tri des canettes et capsules…
Jean-Claude Bernier et Françoise Brénon
Février 2022
Pour en savoir plus
(1) Le dioxyde de carbone, matière première de la vie (dossier pédagogique Nathan / Mediachimie)
(2) (a) La recherche de la composition de l’acier à la fin du XVIIIe siècle ; (b) Aciers sur le site L’Élémentarium
(3) L’hydrogène, une source d’énergie pour le futur (Chimie et… en fiches, Mediachimie.org)
(4) Qu’est-ce que l’hydrogène vert ? (question du mois, Mediachimie.org)
(5) Zoom sur les derniers résultats de la production d’hydrogène « décarboné » (Mediachimie.org)
(6) (a) Les débuts de l’industrie de l’aluminium et (b) Aluminium sur le site L’Élémentarium
(7) Comment faire des casseroles avec la bauxite : l’électrolyse (Réaction en un clin d’œil, Mediachimie.org)
(8) L’électrolyse et les applications industrielles (dossier pédagogique Nathan / Mediachimie)
(9) Recyclage et valorisation des déchets Revue Chimie Paris n°340
Source illustration : PxHere, licence CC0