|
Oui la chimie avance masquée
Rubrique(s) : Éditorial
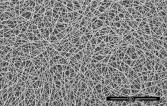
Avec la crise sanitaire occasionnée par le Covid-19 et avec le déconfinement qui s’annonce, la France veut devenir auto-suffisante en masques sanitaires, chirurgicaux mais aussi FFP2 et FFP3 (1). Il existe déjà plusieurs producteurs français Kolmi-Hopen, près d’Angers, qui a reçu récemment la visite du président Macron, Paul Boyé Technologies en Haute-Garonne, Valmy dans la Loire, Macopharma à Mouvaux dans le Nord. Depuis le début de la crise et devant la demande en masques, ils ont accéléré leurs productions, ce qui a permis d’arriver progressivement à 10 millions par semaine fin avril, avec pour objectif 20 millions fin mai puis 40 millions en octobre. Devant la demande importante sur ce marché et avec l’appel à manifestation d’intérêt (AMI) par le ministère de l’Économie, de nouveaux acteurs se lancent aussi dans cette fabrication.
Ce sont à nouveau la chimie, et notamment la chimie des matériaux, qui est alors sollicitée. En effet pour que la France soit indépendante elle doit assurer son approvisionnement en matières premières, en particulier celles qui permettent d’obtenir la composition des 3 couches du masque standard SMS (spunbond-meltblown-spunbond) de tissus non tissés. Or il n’existe qu’une seule unité de production de textile non tissé par extrusion-soufflage (meltblown), Fiberweb, une filiale d’une société américaine située dans le Haut-Rhin, qui annonce investir dans une nouvelle ligne pour tripler sa production, mais qui ne couvrira pas sans doute les besoins des producteurs de masque de l’hexagone.
Deux techniques de production des non-tissés (2) sont possibles :
- l’extrusion-soufflage ou meltblown qui consiste à extruder rapidement un polymère fondu et à le souffler sous forme de fibres, un peu comme on couvre nos greniers de laine de verre en soufflant les fibres pour l’isolation thermique. On utilise des thermoplastiques comme le polypropylène (3) ou le polyester (4).
- l’electrospinning ou électrofilage qui permet l’obtention de micro et même nanofibres par extrusion fine assistée par électrostatique, également à partir de polymères fondus ou en suspension dans un solvant.
Ces techniques sont matures et connues dans l’ingénierie des polymères, la seconde permet l’élaboration de membranes non tissées (5). La maîtrise de la structure des fibres, le contrôle de l’organisation des nanofibres dans la micro-structuration du matériau et la composition chimique à l’échelle de quelques dizaines de microns permettent aussi les applications pour la santé (6). On peut aussi jouer sur les mélanges de polymères hydrophobes ou hydrophiles ; polypropylène, polyimide, sur les électrostatiques ; polyester, acrylique. Selon les combinaisons et leurs tailles, les microfibres ou nanofibres piègent par liaisons de van der Waals ou par électrostatique les gouttes des aérosols et/ou les bactéries ou les virus (7).
Espérons que de nouveaux candidats plasturgistes se déclarent intéressés par ces nouvelles activités, le ministère de l’Économie est prêt à subventionner à hauteur de 30% les investissements encore faut-il assurer l’émergence d’un marché pérenne.
Jean-Claude Bernier et Catherine Vialle
Mai 2020
Illustration : Fibres polymères vues au microscope électronique à balayage (Daltster - travail personnel, CC BY-SA 3.0, Wikimedia)
Pour en savoir plus
(1) Comment fonctionnent les masques de protection respiratoire (sur le site de Pour la Science)
(2) Le textile, un matériau multifonctionnel
(3) Polypropylène (produit du jour de la SCF)
(4) Les chimistes dans l’aventure des nouveaux matériaux
(5) L’intelligence textile (vidéo)
(6) Chimie du et pour le vivant : objectif santé
(7) Electrospinning et nanofabrication pour la santé et l’énergie – ICPEES (CNRS - Université de Strasbourg)